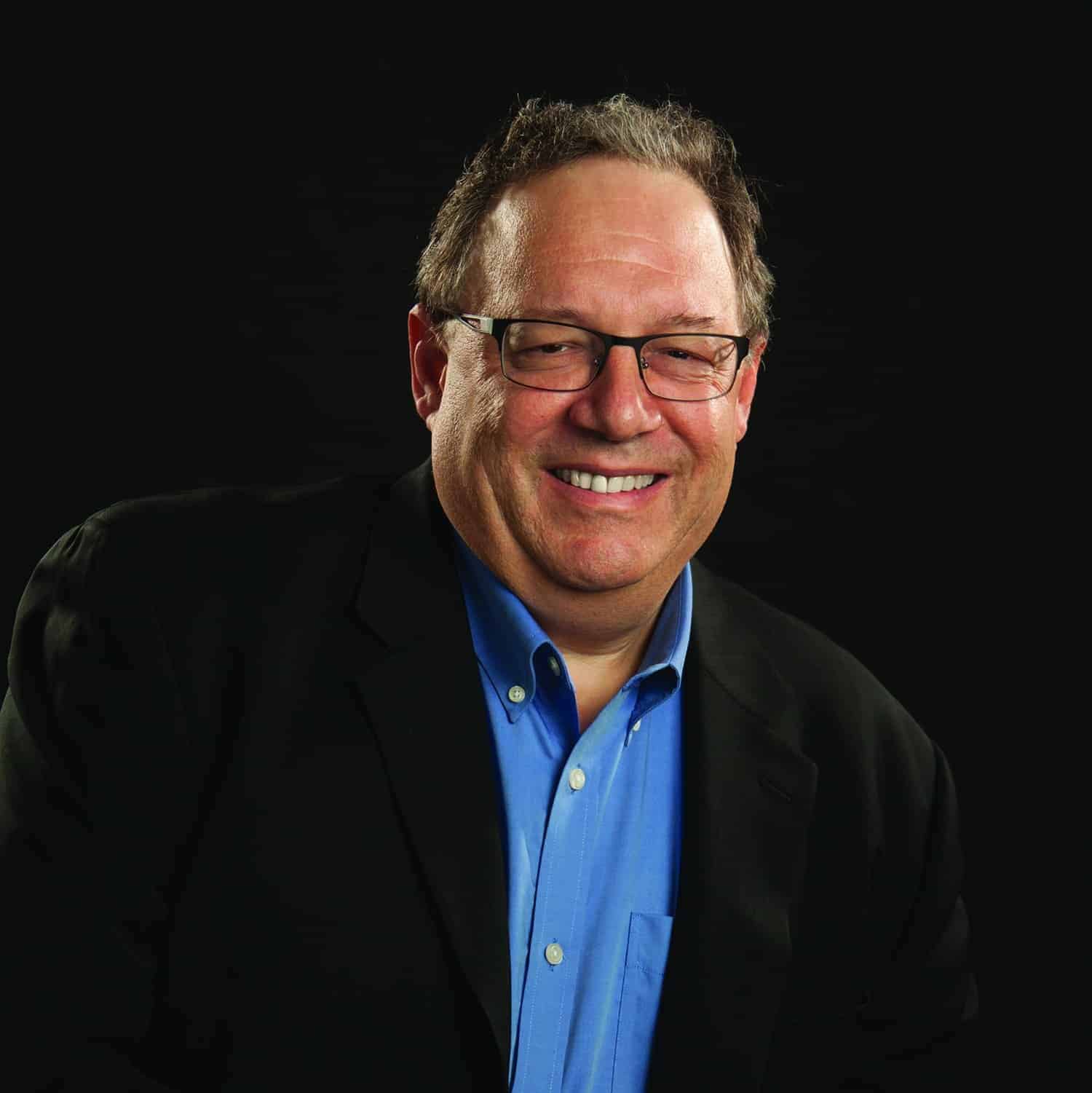
RICH DEPOTO, Business Development Manager, Uyemura
The drive towards high density (HD), ultra-high density (UHD) and alternative substrates, including glass, will be transformative for North American wire interconnection manufacturing in 2025. This paradigm shift requires new equipment, cleanroom manufacturing environments and specially developed chemical processes.
For UBM (under bump metallization), we are approaching the juncture where spacing densities will preclude the use of thick electroless nickel deposit stacks, including ENIG and ENEPIG.
Fortunately, alternative nickel-free Final Finish Deposit Stacks have been on the Technology Roadmap long enough to prove their worth. These final finishes include EPIG and EPAG (Electroless Palladium Immersion Gold and Autocatalytic Gold, respectively), as well as high reliability deposits using IGEPIG (Immersion Gold Electroless Palladium Immersion Gold.)
The ultimate reliability of these new deposits will be determined by the critical electroless palladium diffusion layer, which needs to have low porosity, and therefore good initiation and tight grain structure.
Based on palladium’s low conductivity (< 1.0 x 10 E7 siemens/meter) and the accompanying insertion loss, deposits below 6.0 u inches are most desirable for high frequency designs.
The competitive evolution from mSAP to full semi-additive SAP will also command headlines in the new year. Once PWB manufacturers are comfortable with modified SAP (mSAP), the transition to full semi-additive SAP will occur quickly. The only limits will be a company’s ambition, capital expenditure, acceptable yield threshold, and customer requirements.
Finally, copper surface topography, perennially a high priority, will continue to ascend in importance. As line geometries move below 25 u inches, specialty etchants and organic adhesion promoters will be needed to build these surfaces.
Three processes, each balancing a precise level of etching effect and adhesion, are destined to become commonplace as a result. At the left end of the spectrum is a copper micro-etchant that develops a unique roughened surface and achieves high physical adhesion to a variety of resins, including built-up resin, dry film etch resist, and solder mask.
At the center, a relatedprocess optimizes copper/resin adhesion by coupling an ultra-low etched, unique roughened surface and an organic film. It achieves the highest adhesion to a variety of resins with minimal change in pattern dimensions.
At the elite end of the spectrum, a super-fine copper surface roughness is combined with an organic adhesion promoter to form a perfectly smooth surface, resulting in the lowest signal insertion loss for high frequency circuits.
Click here to read the 2025 Executive Viewpoints in Semiconductor Digest