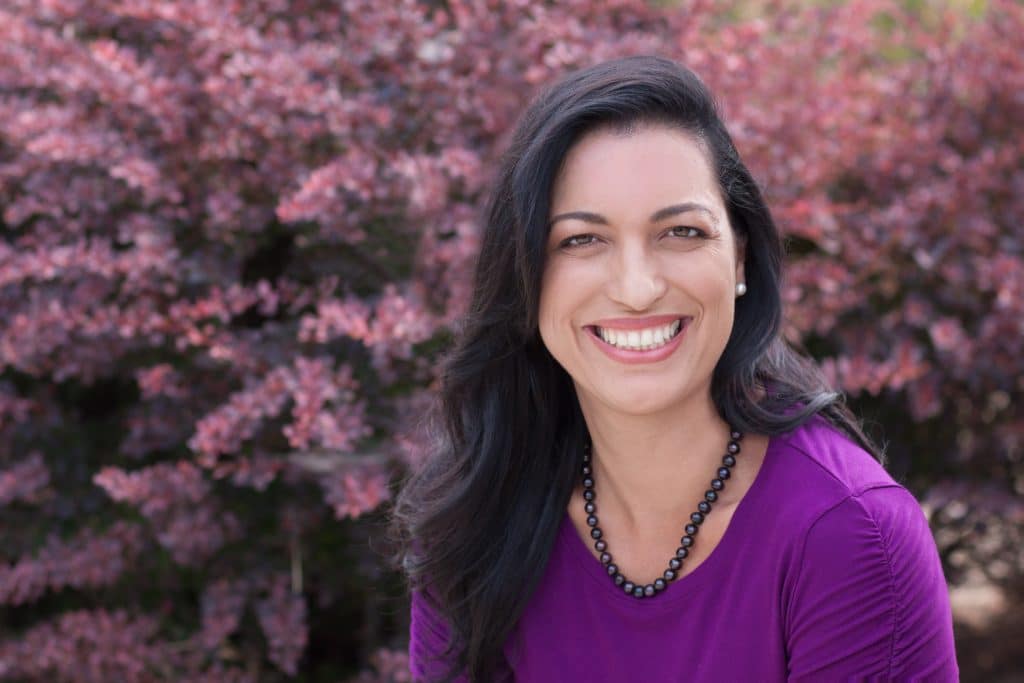
JESSICA GOMEZ, founder and CEO, Rogue Valley Microdevices
I have fond memories of the 90s. This era brought us Nirvana, made flannel cool again, and inspired a generation of women to start careers we didn’t even knew existed. The 90s also saw the first wide scale commercialization of MEMS devices, creating a new branch of the semiconductor industry.
As the MEMS industry began to grow and mature, so did the need for manufacturing these specialized devices, allowing the semiconductor industry to repurpose its otherwise obsolete 100mm and 150mm fabrication facilities. As our big sis, the semiconductor industry began manufacturing on 300mm wafers in the early 2000s, benefiting from economies of scale, design standards, standardized process nodes, and process design kits (PDKs). Meanwhile, the MEMS industry was still finding its footing. Fast forward to today, except in a few cases, the diversity of MEMS design ideas still presents a single product, single process world, resulting in additional engineering effort, time, and expense to bring new devices to market. As the number of 300mm CMOS fabs continues to increase, so does the demand for 300mm-capable MEMS and back-end foundries to support critical technology integration, scalability, and efficiency.
As the CEO of Rogue Valley Microdevices, a MEMS manufacturing company, I view the move to 300mm wafers as a substantial leap forward for the MEMS industry in manufacturing automation and cost-effectiveness, yet many challenges remain. MEMS processing frequently utilizes non-CMOS compatible materials for metallization, sensing and actuation, and hence supporting both CMOS and MEMS manufacturing in the same facility is only undertaken when materials compatibility is possible or dedicated back-end processing cells can be established.
MEMS foundries need to manufacture a high mix of products to ensure facilities run efficiently and at capacity. Highly specialized applications in aerospace, medtech, telecommunications, and automotive industries all look toward 300mm MEMS with a diversity of process needs and designs. We anticipate flexible, 300mm-capable MEMS foundries will play a crucial role to advance the integration of MEMS and microsensors into the supply chain, driving innovation and the development of new, impactful products.
We’re responding to the need for 300mm MEMS with the construction of our second fab, a flexible, 300mm-capable MEMS foundry in Palm Bay, Florida with production set to begin in 2025. We expect to address multiple areas of customer process need, including thin film deposition, through-silicon via (TSV), RDL, UBM, wafer level packaging to propel MEMS and sensor development to unprecedented heights.
Click here to read the 2025 Executive Viewpoints in Semiconductor Digest