Tom Bednarz, Sales Manager Tech Europe, Critical Manufacturing
If you have been running a semiconductor manufacturing execution system (MES) for more than 10 years, you already know well the value of integrated, automated operations. And you likely know also that MES and automation technologies have advanced significantly over the past decade. Maintaining or enhancing those benefits may require migrating to a more modern system. There is, however, more than one way to approach migration, and getting the maximum return on your investment depends on selecting the strategy best suited for your processes, your business and your tolerance for risk. Here are some important things to consider to make your migration a success.
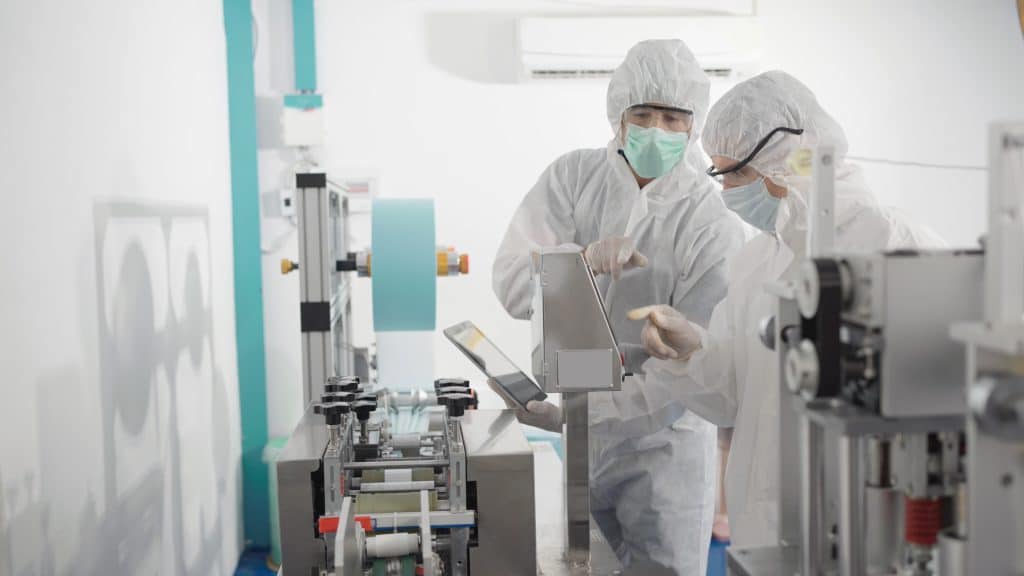
Why migrate?
Migrating to a new MES platform can lower the total cost of ownership of automation and production assets, increase efficiency, revenue, and ultimately, profitability, safety and environmental sustainability.
If your software is at the end of its life and the vendor is phasing out support, you will have little choice but to migrate to a new platform. But even if your ten-year-old system is not on its last legs, there are still major benefits to migrating to a modern system. You can get your legacy functionality in a more robust, cost-efficient platform while also setting yourself up for valuable new capabilities. Here are just some of the MES-enabling capabilities that have matured within the past decade:
Integration with plant devices via IIoT and Industry 4.0.
Streamlined integration with enterprise applications, such as ERP, SCM and PLM.
Advanced machine learning and AI
Advanced simulation and modeling, digital twins
Personalization and customization
Flexibility and scalability
Advanced user interface
Automated regulatory compliance
Cybersecurity
Customization and flexibility
Migration options
Whether you get maximum benefit from your migration depends in part on choosing the migration strategy that is most compatible with your needs. This usually involves making a strategic choice either to migrate everything at once, in phases based on production priorities or in parallel.
Total “big bang” replacement The total replacement model, often called the big bang or rip-and-replace strategy involves disconnecting the legacy system and replacing it with the new one. After preparation and testing, the migration team switches the old system off and the new one on. During the migration, the new MES and master data GUI will sit alongside the operations GUI. They connect to the ERP, to other applications and to a reporting and analytics dataset. Synchronizing the legacy data will usually require application downtime, file change configurations, and application startup procedures. Application migration and process equipment integration happen after synchronizing the operations data.
Phased in migration strategy The phased in strategy involves implementing new MES modules by manufacturing operating units, MES functions or lots.
Phasing in by operating unit involves introducing functional units slowly, and within this option, there are at least also three approaches: phasing in area-by-area, process step by step, or machine by machine, as needed. Regardless of which strategy you choose, the new and old applications must be able to work interchangeably with each other so that you can share and exchange data.
Read the full article in the October issue of Semiconductor Digest.