Bill DeVries, Vice President of Industry Transformation and Customer Success, Dassault Systèmes
The US semiconductor industry is experiencing a pivotal moment as millions of government dollars are funneled toward the creation of more semiconductor manufacturing jobs through the CHIPS Act. While this funding is placing the US on the global semiconductor stage, industry workforce shortages threaten to upend this progress. With this boom, McKinsey forecasts that the US semiconductor industry could see a shortage of 59,000 and 146,000 workers by 2029.
Closing this skills gap is not simply a matter of putting money towards the problem – it requires a collaborative and calculated approach to develop the desired talent. As semiconductors become more cutting-edge, the skills, training, and knowledge required of the workforce producing them must be equally as cutting edge. The bottom line: if a high-tech industry wants to evolve and attract new talent, it should leverage high-tech solutions to develop a workforce that will be equipped to meet the challenge.
Simulation techniques have emerged as an attractive way to train the next generation semiconductor workforce, meaning robust training can take place all from a laptop or mobile device. For example, universities can use this technology to create virtual and interactive replicas of clean rooms to simulate semiconductor manufacturing processes. Students can use this virtual replica to become well-versed with clean room processes and tools, making for a more efficient experience while in the real-life physical space. Moreover, this online training inspires confidence for students in their abilities before entering the physical cleanroom, so time spent outside of the physical space is still being used productively. Universities facing lengthy equipment upgrade timelines can also train students on that equipment in a virtual environment prior to receiving the physical assets. By the time the equipment comes, these students can feel comfortable utilizing it and time is not lost in their studies.
So, how do we make this technology a reality? The answer: virtual twins. In contrast to a digital twin which serves as a direct digital snapshot of an object or space in a moment in time, a virtual twin is a dynamic model, continuously evolving and reacting to a variety of what-if and real-time scenarios. If additional equipment upgrades are made in the real world, virtual twins can be used to prepare and react to them immediately versus having to create an entirely new model which is resource intensive. Virtual twins enable immersive and dynamic training, which are crucial components for upskilling the rapidly evolving semiconductor industry.
While high-tech training options like virtual clean rooms and virtual machines are impressive for universities to tout, it also lowers the barriers to entry for new students to enter the field by making training more accessible. Physical clean rooms can hold a limited number of students at any given time, so utilizing a virtual replica allows for more widespread training when faced with capped resources. In the future as the technology scales, it can be leveraged for on-the-job training as well to train a workforce who are already in the field but want to further develop their technical skillsets.
While the training benefits offered by virtual twin-enabled technology are robust, the key to making them effective long-term is ensuring that they meet the needs of organizations in the industry. This means higher education and employers must be in lockstep if they want to close the skills gap effectively. One approach is for employers to establish partnerships with institutions of higher education to equip students with the type of on-the-job training needed to ensure they feel prepared when entering the workforce. Corporations hold the necessary technology and capital resources to develop the next generation workforce, a task that many higher education institutions are unable to bear alone. Apart from technology and funding, corporations should work with education providers on curriculum that is reflective of their desired industry skillset. The technology is in place – all we need to do now is to make sure it has the infrastructure in place to create sustainable change in the workforce long into the future.
The semiconductor industry is just one example of many industries that stand to benefit from implementing simulation, virtual twin technology into training practices – but it is currently of the most need for change. As higher education continues to adopt this technology and works with employers to ensure it is used effectively to train the next generation of the workforce, the semiconductor skills gap can evolve into a semiconductor skills renaissance.
About the author
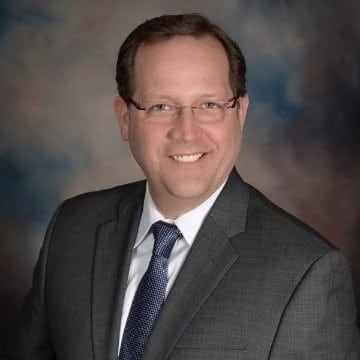
As Vice President Industry Transformation and Customer Success, Bill DeVries is responsible for revenue growth and driving the use of the 3DEXPERIENCE platform. Additionally, Bill is the Senior Director, Academic/Education Sale, North America, where he leads the 3DEXPERIENCE EDU Sales and Workforce of the Future efforts by working closely with prominent Universities, Colleges and technical institutions to develop partnerships, academic Centers of Excellence and continue Dassault Systèmes involvement with institutes or consortia.