JOHN SWAIN, Business Sector Director at Watlow
In semiconductor processing, precise temperature control is essential for producing increasingly sophisticated circuits, particularly as node sizes shrink and chip architectures grow more complex. The role of pedestal heating in maintaining these precise temperatures cannot be overstated, and recent technological advancements are pushing the boundaries of what these critical components can achieve.
One significant development in pedestal heater technology is the shift from traditional single-zone control systems to advanced multi-zone systems. In conventional designs, a single zone would control the entire temperature profile of the pedestal, often leading to uneven temperature distribution across the wafer. Such inconsistencies can result in variations in the film deposition process, affecting the thermal uniformity as well as the ability to set and hold a specific thermal profile to counter other effects within the processing chamber. To address this, multi-zone control systems like Watlow’s POWERGLIDE® have been developed, offering advanced, independent control and tunability over different areas of the pedestal (FIGURE 1).
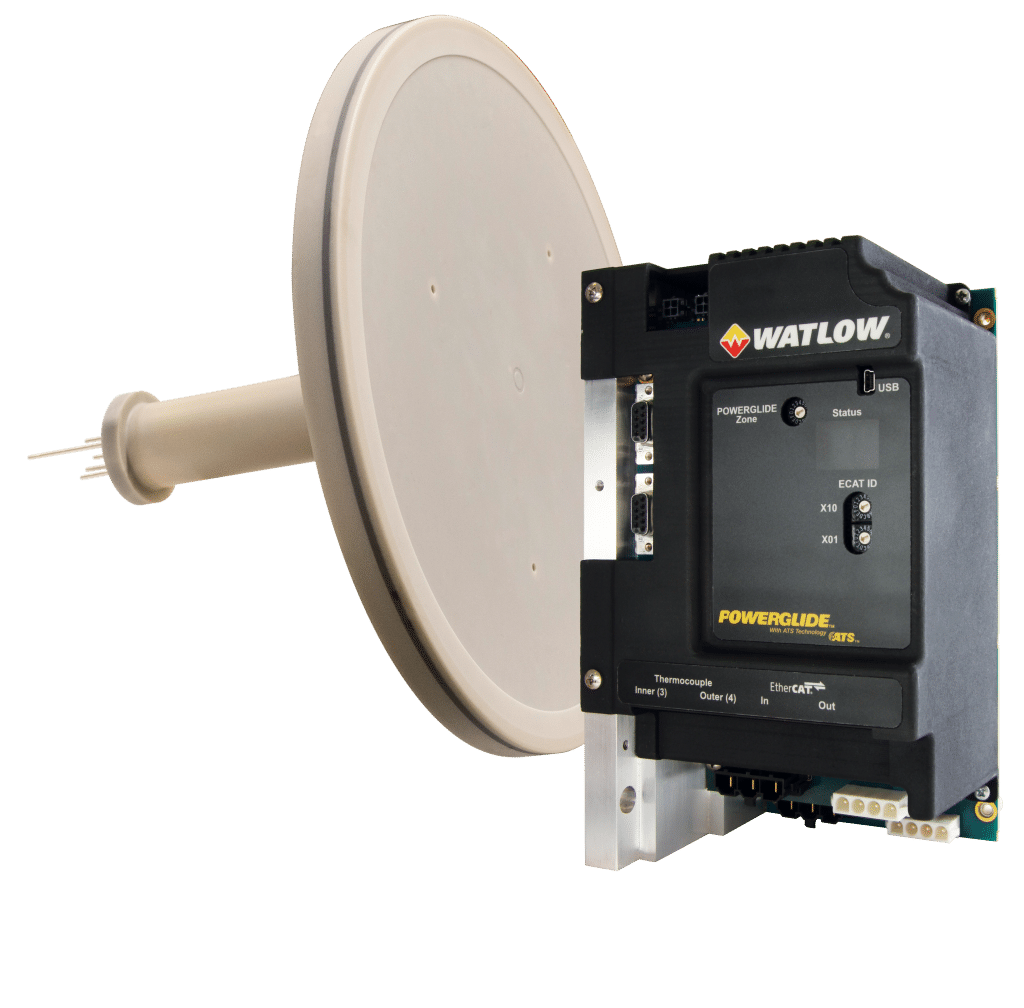
The POWERGLIDE system utilizes high-temperature coefficient of resistance (TCR) heater materials to enable more precise and responsive temperature control. By managing the temperature in multiple zones independently, this system ensures a more uniform thermal environment across the wafer, which is crucial for processes that demand consistency at every step. This level of control not only improves the quality of the semiconductor devices but also enhances manufacturing efficiency by reducing the likelihood of defects and the need for rework. Furthermore, keeping zone temperatures coupled to one another during heat up and cool down increases reliability and ensures fast and safe thermal cycling.
Moreover, the multi-zone approach provides manufacturers with greater flexibility. Different sections of a wafer might require different thermal profiles depending on the specific process being performed. With such systems, manufacturers can fine-tune the temperature in each zone to meet these varying requirements, allowing for more versatile and efficient production lines. This flexibility also reduces the need for specialized pedestals for each process, thereby lowering inventory costs and simplifying logistics.
In parallel with these advancements in control systems, there have been significant improvements in the materials used for pedestal heaters. Traditional pedestal designs often rely on monolithic ceramic structures, which can limit the ability to optimize thermal performance across different parts of the pedestal. To overcome this limitation, Watlow has introduced a bonded ceramic solution that combines multiple layers of ceramic materials, each selected for its specific thermal, mechanical and electrical properties.
For instance, the top layer of the pedestal might be made from a ceramic material with a high-volume resistivity, which allows it to operate at higher temperatures. This capability is increasingly important as the industry moves toward smaller node sizes, which require higher temperatures and electrostatically clamped wafers to ensure optimized film attributes and effective atom excitation during deposition processes. The use of bonded ceramics also enables heat loss management through the pedestal’s shaft by minimizing the thermal gradient between the shaft and the top plate. This improvement leads to more uniform heat distribution across the wafer, which not only enhances the quality of the semiconductor devices but also reduces the risk of cracking within the ceramic—a common issue in high-stress thermal environments.
Customization plays a crucial role in addressing the specific needs of semiconductor manufacturers. Each process might have unique thermal requirements, and the ability to tailor pedestal designs to meet these needs is critical. Watlow’s approach allows for a high degree of customization, from the selection of materials to the configuration of heating zones. This ensures that manufacturers can achieve the precise thermal conditions needed for their processes, leading to better yields, higher quality films and more efficient operations.
Sustainability in semiconductor manufacturing
In addition to these technological advancements, sustainability is becoming an increasingly important consideration in semiconductor manufacturing. Watlow’s refurbishment program is an example of how companies are addressing this need. Over time, the surface of a pedestal can become worn or damaged, reducing its effectiveness. Instead of discarding the entire pedestal, Watlow’s refurbishment service reattaches a new ceramic layer to the existing structure, effectively restoring it to like-new condition. This process not only reduces waste but also lowers costs, aligning with the industry’s growing emphasis on sustainable practices.
The refurbishment process is meticulous. The old ceramic layer is carefully removed, and the underlying structure is inspected for damage. If the base structure is intact, a new ceramic layer is bonded to the top, restoring the pedestal’s thermal performance. This approach preserves the energy and materials invested in the original pedestal while significantly extending its service life. By reducing the need for new pedestal production, this program helps manufacturers decrease their environmental footprint, supporting broader sustainability goals.
The future of semiconductor manufacturing
The impact of these innovations is profound. As the semiconductor industry continues to evolve, with node sizes decreasing and process complexities increasing, the challenges associated with maintaining precise thermal control are becoming more pronounced. Technologies like Watlow’s POWERGLIDE and bonded ceramic pedestals are not just meeting these challenges, they are setting new industry standards. The ability to achieve precise, uniform thermal control across increasingly complex chip architectures will be critical as manufacturers push the boundaries of what is possible in semiconductor design and production.
Looking forward, the role of pedestal heaters in semiconductor manufacturing will only grow in importance. As the industry moves towards even smaller node sizes and more complex processes, the need for advanced thermal management solutions will become ever more critical. Through these advancements, semiconductor manufacturers can achieve the precise control needed for today’s most demanding processes, ensuring the production of high-quality devices that meet the needs of tomorrow’s technology.
In summary, the advancements in pedestal heater technology are playing a crucial role in the ongoing evolution of semiconductor manufacturing. By addressing the challenges of thermal management, reliability, and sustainability, these innovations are enabling manufacturers to meet the demands of increasingly complex semiconductor devices. As the industry continues to push the boundaries of what is possible in semiconductor design and production, advanced pedestal heaters like those offered by Watlow will remain essential components of this progress.