By JOHN R. BEHNKE, General Manager, FPS, INFICON; HOLLAND SMITH, Program Manager Analytics and Equipment Integration, FPS, INFICON; and CHRISTOPHER BODE, Product Manager – Intelligent Manufacturing Systems, INFICON.
The Smart Manufacturing revolution is in full gear within semiconductor manufacturing, and industry leaders are moving quickly to harness the productivity and quality gains it offers. There are also those who are yet to make an investment, and might benefit from the many lessons learned from the early adopters of Smart Manufacturing solutions. This piece will break down the critical elements of a successful Smart strategy and provide recommendations for prioritizing investments that are able to deliver benefit more quickly. These recommendations are based upon real world experiences, including what has worked well (and not so well) in early Semi Smart Manufacturing deployments.
Like any new strategic initiative, the planning phase is essential to the time to realization, success and ultimate return on investment. One early challenge in this process is that there are so many individuals and companies trying to “help” with components of a Smart solution. The volume of claims about knowing exactly the technology, solution space or methodology to become “Smarter” at the Enterprise, Fab, tool, process, and facilities levels can be overwhelming. An accumulation of digital systems, databases and analysis engines in and of themselves will not facilitate the kind of benefits that are possible. Effective solution development rather begins with understanding the fundamental principles of Smart MFG/Industry 4.0, and devising an appropriate strategy for leveraging these available technology and solution partnerships.
SEMI’s Smart Manufacturing initiative is one of its biggest thrusts, and Smart Manufacturing Chapters are now available in most regions to support this focus. SEMI has published an architecture that contains three critical pillars of activity required to create a holistic Smart solution: Sensing, Connecting and Predicting. The key message in the SEMI diagram (Figure 1) is that all three pillars are needed to deliver a high ROI solution. Each pillar is a component within developing a Digital Twin (DT), or what Industry 4.0 otherwise refers to as a Cyber Physical System (CPS). This DT is not simply a database, but rather an integrated platform that can predict and optimize the future state of operations based on a comprehensive knowledge of historical, current and forecasted events. Sensor technology and IOT connectivity, along with increased computing power and analysis technologies, together enable this reality.
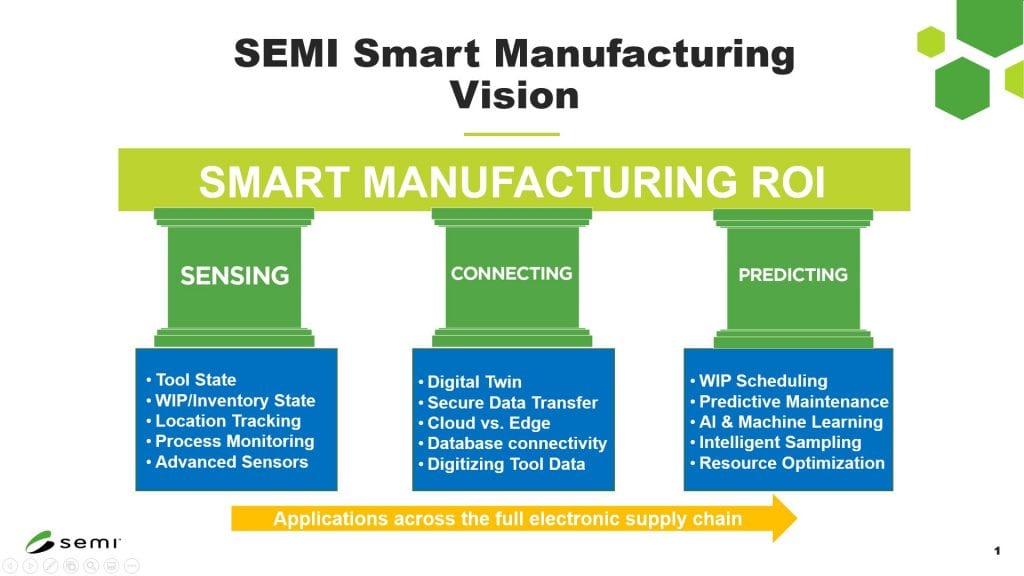
The scope and phased development of new Smart solutions are additional considerations that impact a project’s investment profile. A complete DT solution can provide real-time direction to all fab resources in a globally optimized solution. This should include clear direction to Operations (e.g. operators, tool setup changes, Maintenance staff, etc.), AMHS/WIP movement systems and even Engineering resources based upon the Fab’s current status and priorities. It is also possible to create a smaller DT designed to represent a specific module, tool or process. The investment in terms of the amount of data and connectivity required is smaller, but its recommendations would also be limited to actions taken with the tool/process. Success at a focused level may eventually grow into a fabwide DT, though likely with a longer timeline and higher overall development cost in terms of successive cycles of integration development.
One crucial aspect to consider when developing a Smart Manufacturing strategy is to honestly assess the availability of clean data and information from existing factory systems. Good information is critical even in planning an optimal Smart MFG strategy, which includes understanding investment needs, deliverables and milestones, and ultimately the expected ROI. It is often the case that facilities already have most of the raw data required to start Smart initiatives. The largest task is aggregating and structuring the data properly into the DT. The three main types of digital information required are Flow, State and Requirements/objectives. Flow information details manufacturing methods such as routing, qualified tools and recipes, throughput, cycle time and other such logistical considerations. State information represents the current status of manufacturing assets like tools, recipes, WIP and their location among other states. Objectives include fab goals such as wafer outs, order dates, cycle time, yields and other constraints. For a smaller tool or process-based Smart solution the categories do not change, but the specific information may differ. In all cases, source data availability and management drive the creation of information, and ultimately support the DT and its attendant predictive solutions.
Smart Manufacturing concepts and solutions can be both an exciting opportunity and a daunting challenge to those who are just starting the journey. Those first steps can be critical to early success and demonstrated benefit, and can significantly benefit from beginning with the end in mind. An understanding of Semi Smart Manufacturing principles can help orient an organization in terms of where to start with their Smart plan, as well as what investments are needed when to meet their specific objectives. Finding the right partners and technical solution providers early in the process, and specifically ones with actual demonstrated Smart domain knowledge, is also a major determinant of success as Semi’s needs are unique from other industries. With these considerations in early focus, a transition into Smart Manufacturing is that much smarter.