COURTNEY ERICKSON, Sales Manager & Measurement Expert, Vaisala
Cars. Smartphones. Washing machines. When semiconductor supply chain disruptions spurred a shortage of everything from automobiles to consumer electronics, the U.S. government launched a multibillion-dollar effort to bring chip manufacturing back to the States. With manufacturing capacity projected to triple by 2032, the American semiconductor industry must scale to meet this expanded demand.
Given this recent push to revive domestic chip production, manufacturers face mounting pressure to maximize yields, maintain consistent quality, and improve energy efficiency — all while producing the increasingly sophisticated chips powering consumer electronics, critical infrastructure, and the technologies that will shape our future.
Semiconductor production, however, requires exceptionally controlled environments, as even slight fluctuations in humidity and temperature can severely impact chip quality, exacerbate energy use, and lead to costly financial losses. While costs vary depending on the chip’s complexity and manufacturing process, every defective chip represents a missed revenue opportunity.
The industry’s massive growth potential — driven by the CHIPS Act and broader reshoring initiatives — highlights the critical need for more precise process control in semiconductor fabrication.
Challenges in semiconductor manufacturing
Pursuing perfection in modern semiconductor facilities presents technical challenges — and a financial necessity. While many fabrication facilities currently achieve yield rates between 35% and 70%, the industry continually strives toward the ambitious goal of 100% yield — where every chip on a wafer functions as intended. With individual wafers potentially costing as much as $30,000 in the near future, even fractional yield improvements can translate to millions of dollars in savings for large-scale manufacturers.
A delicate balance of precision and consistency, modern semiconductor production sees the most advanced chips feature transistors that measure just a few dozen nanometers — just a fraction of the size of a human hair. At this microscopic scale, environmental variations otherwise imperceptible in most other manufacturing processes can ultimately compromise computer chip functionality.
Just slight variations from optimal environmental conditions can result in defective chips or batch failures, causing significant delays and financial setbacks. High humidity can introduce impurities, leading to defects. Similarly, temperature instability can cause inaccurate humidity readings, inconsistent product quality, and reduced reliability. Beyond product quality concerns, manufacturers prioritize energy efficiency to an increasing extent, as poorly controlled humidity levels strain resources and increase costs.
With some semiconductor fabs consuming as much electricity as small cities, overdrying or inconsistent humidity control can escalate energy consumption to the point of hundreds of thousands of dollars in unnecessary operational expenses.
Read the full article in Semiconductor Digest magazine.
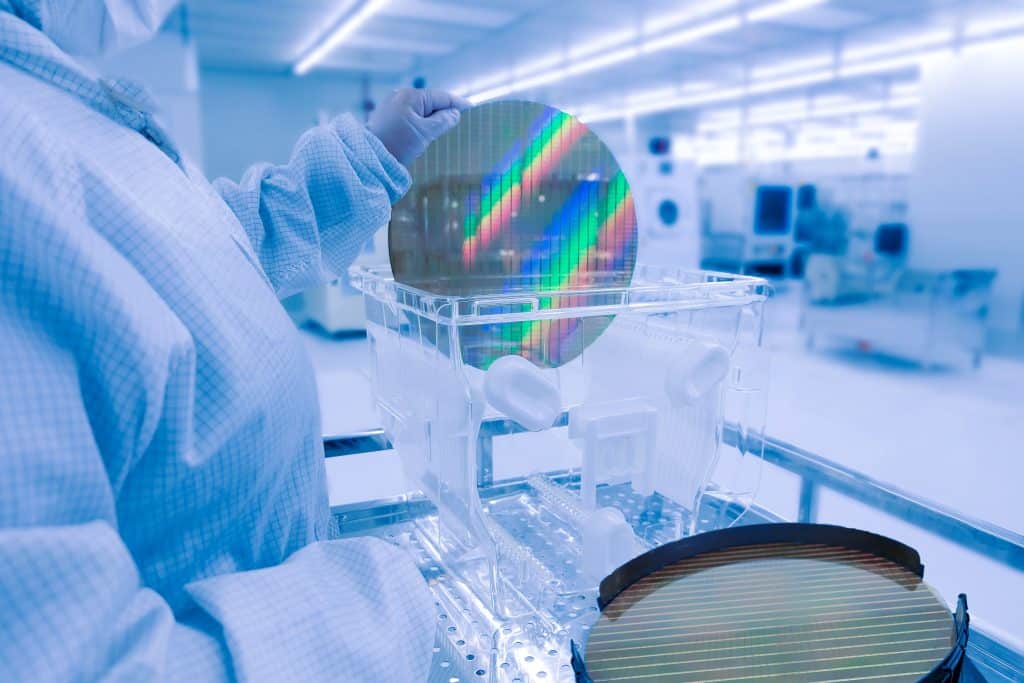