Power electronics are at the heart of many electronic systems in battery-electric vehicles. Here, semiconductors manage the energy and ensure that it is utilized as efficiently as possible. MOSFETs (metal-oxide-semiconductor field-effect transistors) made of silicon carbide (SiC) are renowned for taking electromobility to new levels of efficiency. While semiconductor technology is already widely used in some areas, its application is still in its early stages in certain automotive applications. The semiconductor manufacturer and automotive expert Bosch has an optimistic outlook on the future of silicon carbide.
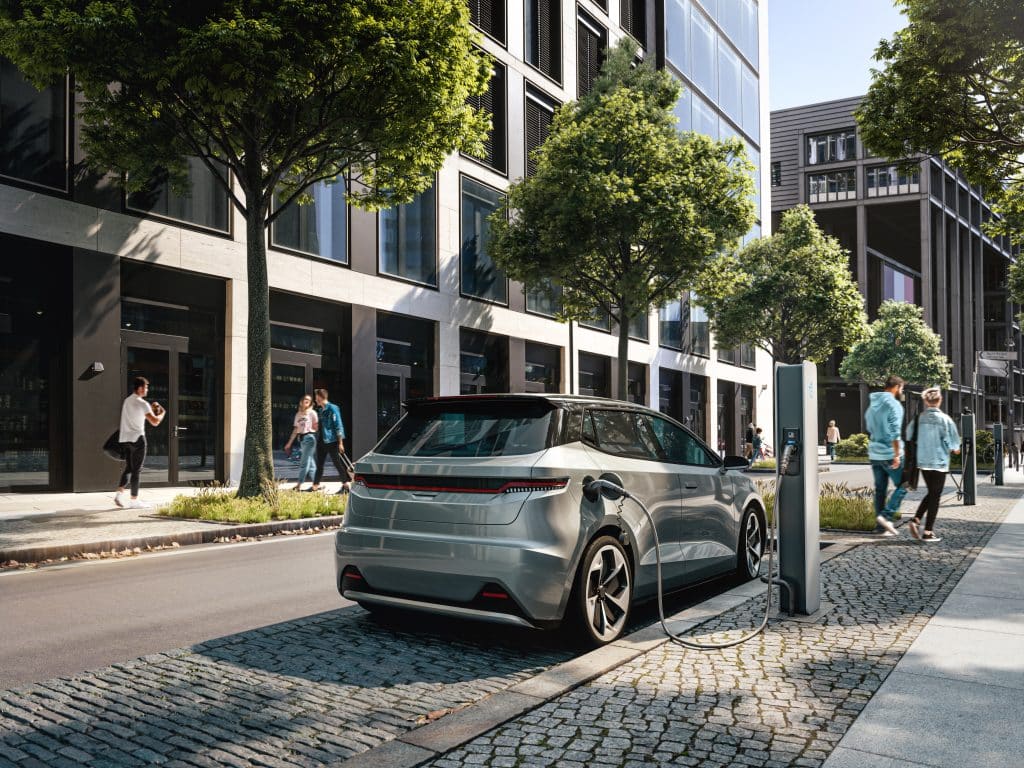
Silicon carbide belongs to a class of materials known as wide bandgap semiconductors. This wider bandgap offers several advantages over silicon: thanks to the higher breakdown field strength, these special semiconductors can block higher voltages with lower on-state resistances, making them ideal for the high-voltage range. In addition, the improved temperature stability ensures that the semiconductor retains its performance even at temperatures of up to almost 400 degrees Fahrenheit. Another key advantage of SiC is its higher charge carrier mobility, which enables significantly higher switching frequencies compared to conventional silicon-based solutions. Together, these benefits lead to improved overall efficiency.
Why SiC is worthwhile
The main benefits of silicon carbide vary depending on which vehicle components the chips are used in. In electric vehicles, SiC primarily enhances power electronics, especially the inverter, the DC/DC converter, and the on-board charger. The use of SiC in the inverter enables higher efficiency, which increases the driving range.
SiC MOSFETs have higher switching transients than Si-IGBTs, allowing for quicker switching speeds. By increasing the switching speed, the overall switching loss is reduced by around 50 percent. Additionally, SiC technology enables higher switching frequencies, reaching up to 24 kHz.
The capability significantly benefits DC/DC converters and on-board chargers by enabling more compact and lightweight systems with improved efficiency. Inverters equipped with SiC semiconductors enhance the overall efficiency of electric drives, reducing electrical consumption (kWh per 100 km) in conjunction with other improvements in the overall system. This increases the range of electric vehicles or, in other words, allows the battery capacity to be optimized based on the vehicle class and application to save costs.
SiC chips are conquering the market
Despite their numerous advantages, not all electric cars currently contain silicon carbide chips. One reason is that SiC semiconductors are more expensive than comparable silicon components. The production of silicon carbide boules requires very high temperatures – around 3,600 degrees Fahrenheit – and over ten mask or structure levels with more than 300 process steps are needed before the raw material turns into a chip. As a result, the use of silicon carbide generally follows a careful cost-benefit calculation.
Inverters based on silicon carbide technology are therefore currently found primarily in high-performance vehicles, where the benefits of SiC semiconductors are most obvious. “In smaller electric vehicles, which often use 400-volt batteries, silicon-based IGBT modules are still common in inverters. However, in vehicles which are based on 800-volt technology, the advantages of silicon carbide in the inverter clearly outweigh the disadvantages,” explains Anne Bedacht, Head of Product Management for Power Semiconductors at Bosch.
For her, efficient e-mobility is therefore closely linked to SiC: “If you look at the progress made in both SiC and electric vehicles over the last ten to fifteen years, it’s undeniable and continues to evolve. Silicon carbide chips have been conquering the market for several years, starting with the most profitable applications. As production scales up, the cost of these chips will eventually decrease – making their use increasingly worthwhile across more vehicle components and models.”
Read the full article in the October issue of Semiconductor Digest.