By Johanna Brown, Product Manager, Structural and Engineered Components, Greene Tweed
Within semiconductor wafer cleaning, harsh chemicals and elevated temperatures can cause components to crack, leak, or mechanically fail (before the expected component lifetime). Downtime in semiconductor chip manufacturing or subsequent damages that may occur during production are hefty bills to swallow. OEMs and Fabs want to avoid this.
How do you improve the lifetime and reliability of wet chemical wafer cleaning components? This question prompted a leading semiconductor equipment manufacturer to reach out to Greene Tweed.
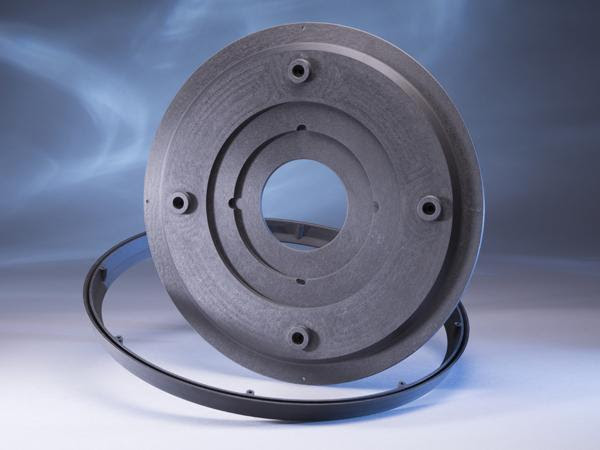
Problem statement: Harsh cleaning chemistries were problematic to the current component design, realizing leakage and component lifetime was not as expected
Solution: Eliminate the issue and improve the lifetime and reliability of this equipment with a Greene, Tweed solution
Greene Tweed’s team of engineers collaborated with the OEM’s engineers for an ingenious solution: Replace their existing multi-piece assembly with a single piece integrated solution, eliminating the potential for leakage at component interfaces. Greene Tweed offered a consolidated, engineered designed solution made from ONX®600, our semiconductor grade material. It’s easy to see how an integrated design (made from a resilient material) would improve lifetime, reliability, and mitigate leakage issues.
Let’s delve into what made ONX®600 the ideal choice. ONX®600 is an ultrapure (low metal and ion content) fluoropolymer-based, carbon fiber reinforced composite. It is a high-performance material with superior mechanical wear properties at ambient and elevated temperatures (500°F/260°C). ONX®600 is chemically resistant to strong acid chemistries such as SPM (sulfuric-peroxide, Piranha), SC1 (ammonium hydroxide-peroxide), SC2 (HCl-peroxide), and dilute HF cleaning solutions and is electrically conductive to remove static charges caused by spin-spray actions (protecting delicate features of semiconductor devices).
After two years of project testing and field trials, the ONX®600 single piece integrated solution has delivered superior performance and has successfully been qualified for use on new equipment builds. The new design has been adopted, and the customer reports up to 4x improvement in mean time between replacement (MTBR) in applications using the harshest chemicals!
The semiconductor equipment maker working with Greene Tweed is not unique. Mitigating issues, reducing particle formation, and extending MTBR/MTBF are significant issues for any wet processing OEM or fab. These tools, crucial in achieving high precision wafer fabrication processes, remain vital for increased yields and reliability, especially for advanced nodes.
Greene Tweed eagerly works with our customers to optimize solutions to meet the application’s requirements. Our goal is to provide engineered solutions to reduce downtime, eliminate problems, and provide our future partners a seamless transition to gain the values and benefits of working with Greene Tweed.
Do you have a similar design challenge you need to overcome to improve the reliability of your wafer processing system? Please reach out to a Greene Tweed representative to explore what GT engineering can do for you.