Researchers have developed an ultra-thin and ultra-flexible electronic material that could be printed and rolled out like newspaper, for the touchscreens of the future.
The touch-responsive technology is 100 times thinner than existing touchscreen materials and so pliable it can be rolled up like a tube.
To create the new conductive sheet, an RMIT University-led team used a thin film common in cell phone touchscreens and shrunk it from 3D to 2D, using liquid metal chemistry.
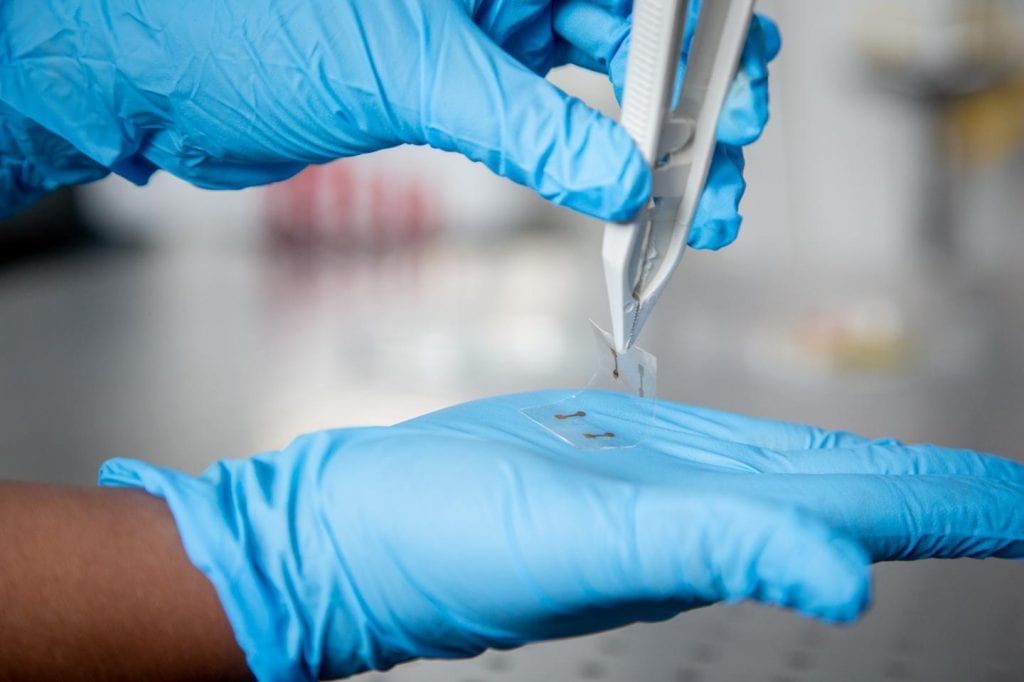
The nano-thin sheets are readily compatible with existing electronic technologies and because of their incredible flexibility, could potentially be manufactured through roll-to-roll (R2R) processing just like a newspaper.
The research, with collaborators from UNSW, Monash University and the ARC Centre of Excellence in Future Low-Energy Electronics Technologies (FLEET), is published in the journal Nature Electronics.
Lead researcher Dr Torben Daeneke said most cell phone touchscreens were made of a transparent material, indium-tin oxide, that was very conductive but also very brittle.
“We’ve taken an old material and transformed it from the inside to create a new version that’s supremely thin and flexible,” said Daeneke, an Australian Research Council DECRA Fellow at RMIT.
“You can bend it, you can twist it, and you could make it far more cheaply and efficiently that the slow and expensive way that we currently manufacture touchscreens.
“Turning it two-dimensional also makes it more transparent, so it lets through more light.
“This means a cell phone with a touchscreen made of our material would use less power, extending the battery life by roughly 10%.”
DIY: a touchscreen you can make at home
The current way of manufacturing the transparent thin film material used in standard touchscreens is a slow, energy-intensive and expensive batch process, conducted in a vacuum chamber.
“The beauty is that our approach doesn’t require expensive or specialised equipment – it could even be done in a home kitchen,” Daeneke said.
“We’ve shown its possible to create printable, cheaper electronics using ingredients you could buy from a hardware store, printing onto plastics to make touchscreens of the future.”
Thick and thin: how to turn an old material new
To create the new type of atomically-thin indium-tin oxide (ITO), the researchers used a liquid metal printing approach.
An indium-tin alloy is heated to 200C, where it becomes liquid, and then rolled over a surface to print off nano-thin sheets of indium tin oxide.
These 2D nano-sheets have the same chemical make-up as standard ITO but a different crystal structure, giving them exciting new mechanical and optical properties.
As well as being fully flexible, the new type of ITO absorbs just 0.7% of light, compared with the 5-10% of standard conductive glass. To make it more electronically conductive, you just add more layers.
It’s a pioneering approach that cracks a challenge that was considered unsolvable, Daeneke said.
“There’s no other way of making this fully flexible, conductive and transparent material aside from our new liquid metal method,” he said.
“It was impossible up to now – people just assumed that it couldn’t be done.”
Patent pending: bringing the tech to market
The research team have now used the new material to create a working touchscreen, as a proof-of-concept, and have applied for a patent for the technology.
The material could also be used in many other optoelectronic applications, such as LEDs and touch displays, as well as potentially in future solar cells and smart windows.
“We’re excited to be at the stage now where we can explore commercial collaboration opportunities and work with the relevant industries to bring this technology to market,” Daeneke said.