VIDYA VIJAY, Senior Product Line Manager, Nordson Test & Inspection
Mirrored in almost every sector, manufacturing is undoubtedly entering a new era of productivity, centered on – and shaped by – smart, automated, interconnected ecosystems. With additional pressures due to consumer demand, semiconductor fabs are rapidly advancing toward ultra-efficient seamless workflows that enhance precision, productivity and ultimately, profitability.
Widely hailed as the ultimate benchmark for production efficiency, the concept of the fully autonomous ‘dark factory’ is steadily evolving from aspiration to a tangible objective in modern production strategies. This heavily impacts modern innovations, particularly in semiconductor production, where the focus is on unlocking next-level automation, minimizing operator dependence, and streamlining production processes. By reducing the need for on-site operators and enabling real-time data exchange across systems, fabs are laying the groundwork for a future where highly autonomous production becomes the norm – whilst optimizing processes and returns in the shorter term (FIGURE 1). This gradual evolution is helping semiconductor manufacturers tackle the complexities of modern production while positioning them to meet the growing demands for faster, more precise, and cost-effective chip manufacturing.
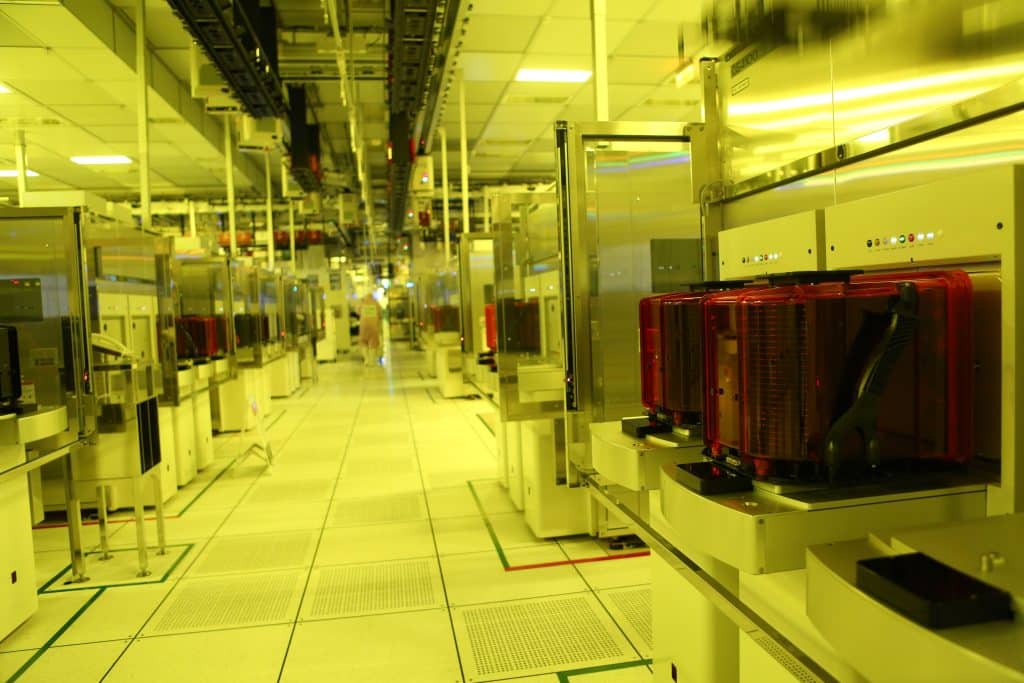
Crucially, however, quality control systems are providing the critical missing link in this journey toward full automation. Semiconductor manufacturing, by its very nature, demands extreme precision and constant monitoring of equipment, with tools such as sensors and measurement solutions ensuring these requirements are consistently met. By enabling real-time process adjustments and maintaining tight tolerances, these technologies bridge the gap between advanced automation and the uncompromising standards of modern chip production. As fabs progress toward greater autonomy, the integration of cutting-edge quality control systems will be essential in the manufacturing ecosystem of tomorrow.
Future-proofing fabs: the power of predictive metrology in semiconductor manufacturing
While metrology isn’t a new field, historically, the need to open tools for manual measurement or inspection creates significant bottlenecks in production, often requiring stoppages, disruption of vacuum environments, and extended pump-down times before production can resume. For the industry to evolve and meet rising demands, the sensors and measurement technologies that support these processes must evolve as well. Thankfully, these challenges, and the increasingly demanding landscape of modern semiconductor manufacturing, are now being met head-on with cutting-edge innovations, welcoming the rise of advanced sensors that are not only shaping the long-term future of semiconductor manufacturing but also delivering critical efficiencies in the near term. These innovations, designed to unlock the power of predictive metrology, are enabling real-time, non-contact measurements that streamline operations, reduce downtime, and support the seamless automation that is essential for keeping pace with modern production needs. Aspects of the production line from chemical vapor deposition (CVD) to etching processes can now be integrated with advanced sensors to ensure the meticulous adherence to strict controls and ensure a more connected, streamlined production environment – ultimately boosting throughput.
Quality control unplugged
The ability of these sensors to deliver wireless and instantaneous measurements makes them an even more valuable pillar of the modern factory floor, particularly as manufacturers look to the future of lights-out production. With wireless, vacuum-compatible measurement, real-time feedback and predictive maintenance capabilities, next-generation sensors from Nordson are ideally positioned to keep pace with a rapidly evolving industry landscape and address the manufacturing challenges of tomorrow (FIGURE 2).
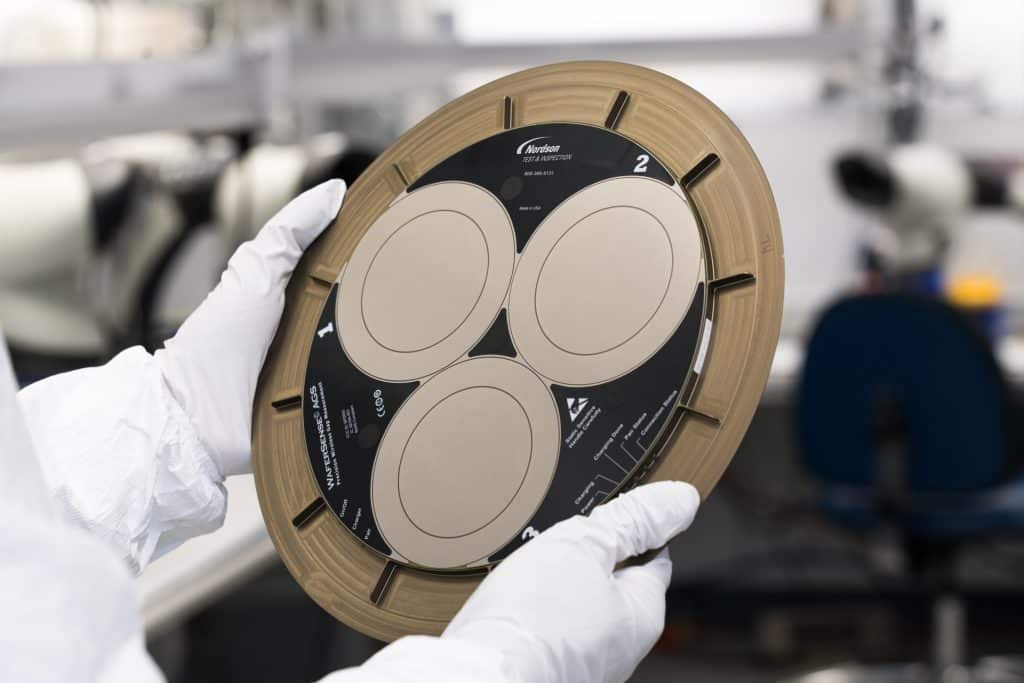
Achieving next-level precision, however, hinges on controlling even the most complex parts of the production line, such as deposition processes (FIGURE 3). Micron-level control over material layering is vital for ensuring optimal device performance and reliability, requiring advanced measurement and feedback systems. Gapping sensors play a vital role in this control, providing real-time data to ensure uniform film thickness, optimize deposition accuracy, and enhance yield while minimizing defects and waste.
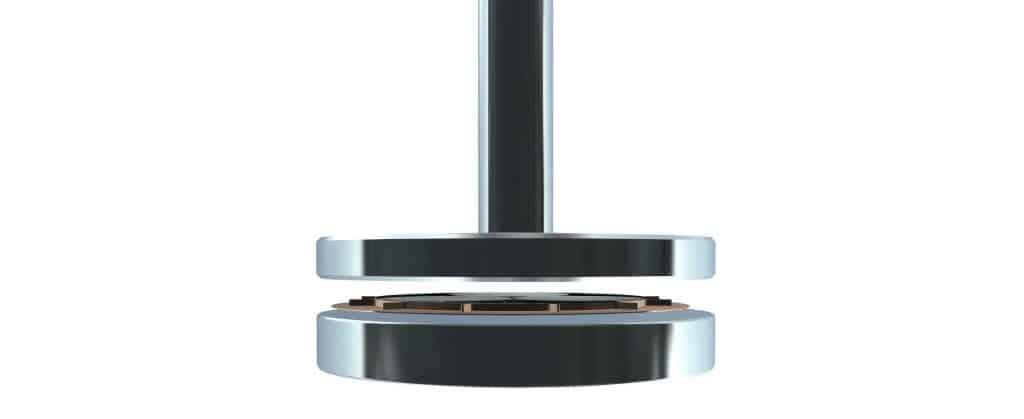
Click here to read the full article in Semiconductor Digest magazine.